The future of freight: NWTF team design AI-assisted, moveable flaps to cut aerodynamic drag on trucks
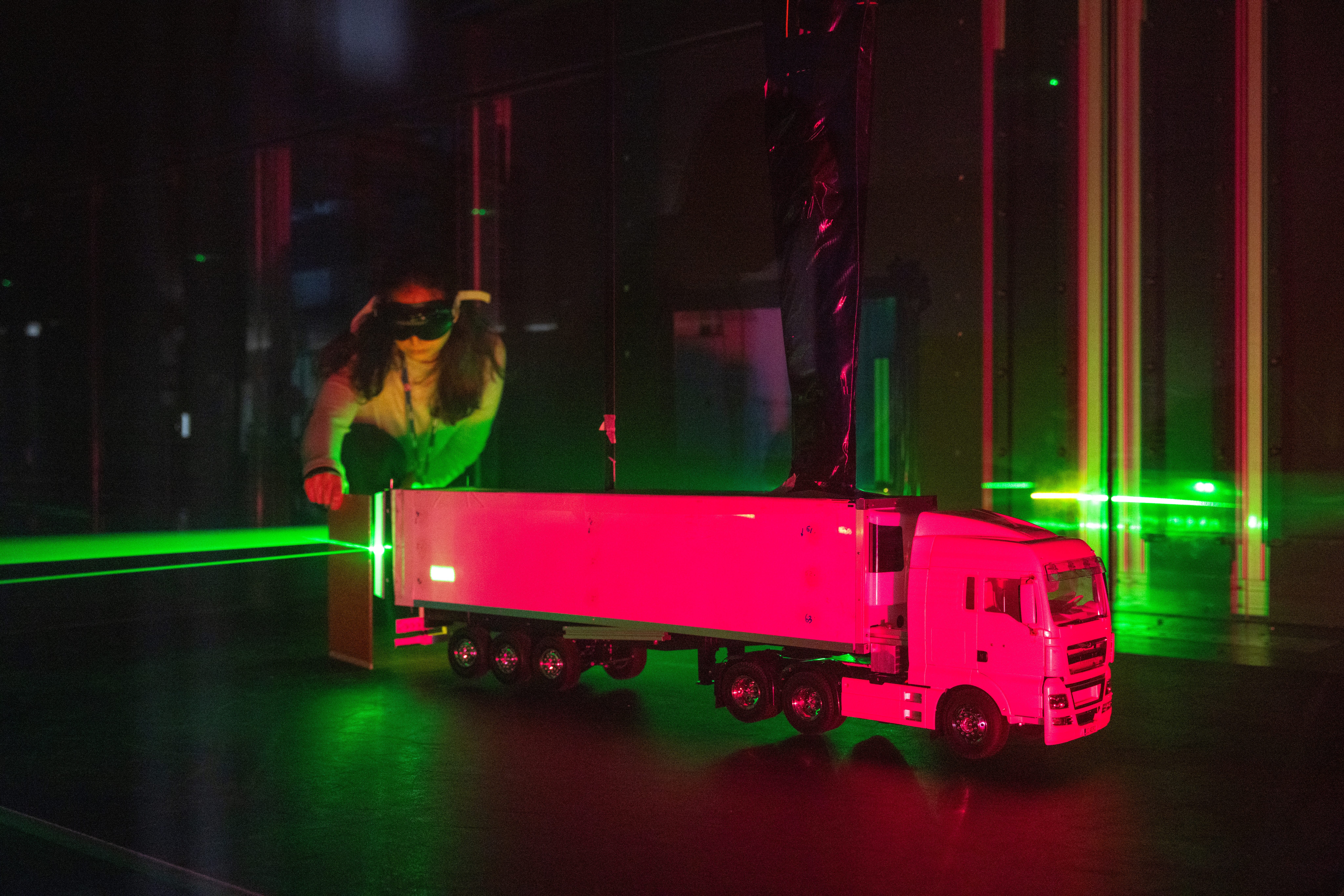
A research team at the National Wind Tunnel Facility (NWTF) has characterised the dynamic air flow around a scale model truck, informing the design of intelligent, adjustable flaps to reduce drag and cut fuel consumption.
Transport is responsible for around one-fifth of global CO2 emissions, with passenger vehicles contributing around 45%, freight trucks 29% and aviation 11%. A major focus of research goes into developing new modes of propulsion, replacing the combustion of fossils fuels with full electrification or technologies like hydrogen fuel cells. But there are other ways to improve efficiency and conserve either fuel or battery power, by looking at aerodynamics. For freight trucks with combustion engines, it has been estimated that about 65% of the total fuel is consumed by aerodynamics drag. Consequently, a 20% reduction in drag corresponds to a 10% saving on fuel. Certainly not an insignificant efficiency when looking at the global industry as a whole.
A knotty problem to untangle
A team of researchers at Imperial College London are investigating aerodynamic strategies at the National Wind Tunnel Facility (NWTF) as part of a wider project around AI for NetZero. The team is led by Dr Georgios Rigas (Reader) and Dr Isabella Fumarola (Research Fellow) – alongside Dr Xianyang Jiang (Research Associate), Dr Max Weissenbacher (Research Associate) and Junjie Zhang (PhD student).
Dr Isabella Fumarola gives some insight into the complexities of freight aerodynamics specifically:
“Air flows over and around the truck and then detaches as it passes the rear of the vehicle, causing a sudden drop in pressure and energy efficiency. This detachment creates a highly dynamic and chaotic flow, filled with swirling air structures – much like the patterns seen in cigarette smoke. From an aerodynamic perspective, the key challenge is identifying where energy is being lost. These large, moving air structures play a significant role in energy loss, and minimizing their impact is crucial.”
Yet, it’s difficult to safely and comprehensively analyse the aerodynamic flow around a full-sized truck on a real road. Even if you were to use escorting cars and vehicles mounted with sensors, following alongside a truck, it would give a rather limited picture.
Unique experimental set-up
Using the 10×5 Wind Tunnel at the Imperial node of the NWTF, the team have assembled a truly unique experimental set-up including a scale model of a truck, running on a movable track (like a treadmill) coupled with an advanced sensor array. They are also able to simulate various weather conditions, including cross-winds coming from different directions.
The team have adapted a technique called volumetric Particle Tracking Velocimetry (PTV) to analyse flow dynamics in high resolution. This involves flooding the wind tunnel with helium-filled bubbles (like soap bubbles, but lighter) that act as tracers. They then illuminate these bubbles with powerful LEDs and track them with four synchronized cameras, building up a picture of how individual particles move through the entire volume of space.
Whilst the truck is in the wind tunnel, the researchers also manually adjust the angle of the four static flaps on the trailer to identify the best configuration for energy saving.
Smart, real-time adjustments
All this research helps to build up a very detailed body of knowledge about the aerodynamics of a moving truck – which would be an impressive enough feat on its own. But the team is aiming to go even further. The ultimate goal is to use this knowledge to design ‘smart’ flaps that automatically and rapidly change angle in real-time to reduce drag. This is done with the help of a technique called reinforcement learning (RL), a type of AI. The idea is that sensors mounted on a moving truck gather data to be interpreted by the RL-algorithm, which then makes a decision about the best angle to position the flaps at each instant in time, in order to minimise aerodynamic drag.
Before trying to do this on a real-sized truck, these intelligent flaps can be trialled in the wind tunnel, as Dr Fumarola explains in more detail:
“The first step in developing our reinforcement learning system is understanding the physics of flow – identifying the dynamics, such as the frequencies at which turbulent structures move. Training the algorithm is a meticulous process, taking up to 12 hours to define and optimize the parameters it needs to control, such as drag measured by load cells or pressure sensors. The system is then evaluated and fine-tuned to achieve the best possible performance.
“Next, we test its adaptability to changing conditions. For example, we train the algorithm without the rolling road active, then introduce it to see if it can adjust and maintain its effectiveness in a dynamic, real-world scenario.”
Making a compelling case to industry
The team is still experimenting with different flap configurations and lengths – but they also have to bear in mind what is likely to be acceptable and practicable for industry. While there are several stages remaining before a viable commercial product is ready, the team is confident that their prototype system will be a compelling offer to the freight industry – which has shown a willingness in recent years to adopt new innovations such as the ‘bow-tail’ design seen on some trailers. Indeed, in 2022 regulation change allowed the use of aerodynamic features on heavy goods vehicles (HGVs) for the first time in the UK, aligning with practices already common in the US. The UK government estimates that aerodynamic improvements to HGVs could result in fuel savings of between 7% and 15%. For global freight operators, even a 5% reduction in fuel consumption could translate into billions in savings annually.
Crucially, part of the NWTF’s mission is to establish closer ties with industry, creating a pull-through environment and an intended spill-over of the collaboration and benefits to other sectors.
Dr Fumarola comments: “The NWTF has been instrumental for our project. Its state-of-the-art equipment and collaborative environment allow us to conduct advanced experiments, such as using rolling roads to simulate real-world conditions. This kind of research pushes us closer to practical applications and potential commercialization.”
By bridging cutting-edge research with practical application, this project demonstrates how AI can revolutionize transport, delivering both environmental and economic benefits.
This research has been funded through the UKRI AI for Net Zero grant “Real-time digital optimisation and decision making for energy and transport systems” (EP/Y005619/1).